
Identifying the Source of the Problem and Why it’s Important
Labels are essential to making products stand out against their competitors. It is oftentimes the first thing customers look at when deciding to purchase a new product. But what if the label looks bad after application?
It could be one of a variety of issues. It could be the applicator machine, the labels, environmental conditions, or something else. Perhaps your labels always seem to tear or fall off the product. It could be the adhesive, the material, or the shape.
None of these issues are out of the norm. There are millions of labels successfully attached to their products every day. While these issues can be frustrating and time-consuming, there is oftentimes an easy solution. Below are six of the common issues expressed during the labeling equipment process and how they can be solved.
Problem #1 - Environmental Label Application Problems
The application environment of your labeling process makes a huge difference in whether or not it will stay on successfully. Many labels are climate-sensitive.
- Too humid – Moisture degrades the adhesive and may cause peeling
- Too cold – Labels become stiff and the adhesive can become ineffective
- Too warm –Labels may peel or not stick to the container
If you are operating equipment year-round in a warehouse, you may experience a lot of these labeling application problems. Especially if there isn’t strong climate control, the work of your labeling equipment may be compromised by drastic weather, such as cold winters and hot humid summers. This may include labeling applicator jams, poor dispensing, labels sticking to the wrong object, peeling, curling, or labels falling off.
Creating the Right Environment for Label Application
For hot and humid conditions, try storing labels in lower areas. Heat rises and sometimes the higher shelves can be as much as 20-30°F hotter than those beneath it. To protect the contents from humidity, store labels in airtight plastic bags. One additional tip for rolls of labels is to store them with the hole placed vertically. This will prevent labels from sliding on the liner.
If you are experiencing labeling issues due to damp or cold conditions try to bring the contents of your container to room temperature before labeling. You should also try to keep the labels themselves stored at room temperature. Lastly, make sure all containers are dry and clean before applying the label.
Problem #2 - Label Conversion Quality Problems
Some labels may be pressure-sensitive. If not dealt with correctly, this could lead to label application problems. For this reason, manufacturers often use a process called “label conversion.” This is where a master roll of the substrate is created by applying adhesive, and a liner that has been coated with a release agent is added. This substrate is then guided into the press for printing and converting. A die cutter makes a precise incision that goes through the label layer but not through the base layer, and a rewinder creates the finished roll.
While this isn’t an abnormal process, Labels & Labeling magazine studies suggest nearly 50% of quality faults in pressure-sensitive labels that result in downtime are related to this converting process.
Some issues may include die strikes being too deep or not deep enough because of an error during the conversion process. This can cause a couple of different issues:
- Too deep – Deep die strikes may expose the glue to the liner and make stripping difficult or impossible
- Too shallow – Shallow strikes do not cut through and may prevent labels from peeling off the roll
Another common problem with the die may occur if cutting heads are too dull. This will require more forceful die strikes to occur to make cuts. Sometimes the added force unintentionally penetrates the protective silicone layer which is used to keep the label from bonding to the liner, causing an inability for a clean release. If the face material becomes mismatched, you may experience additional label application problems once it reaches the end user.
One last common issue related to conversion quality for labeling equipment use is the increased difficulty of peeling labels. On the flip side of this, users may experience labels lifting or dropping off as they make their way through labeling equipment. These issues are likely due to insufficient quantities of release agents.
Identifying the Issue with a Label Converter
No matter what the issue may be, an experienced label converter should be able to help you identify the roots of these issues and help you work through them. Work with them to find out if maybe it is a climate issue or material issue that’s related to the production environment.
If the issue seems to align more with something die-strike-related, there is an additional hack you can try. Try coloring the backside of the liner with a marker. If the ink bled through once the label was removed, this means the silicone layer is damaged. To fix this issue, talk to your converter and request a replacement for the faulty roll.
Problem #3 - Container Irregularities
Sometimes the issue is not specifically related to the label itself. If you notice your labels are frequently becoming loose or wrinkling, the problem may have to do with the container it is being applied to. Even small irregularities, such as ridges or shape variations, may lead to voids beneath the label. This may prevent them from sticking.
Finding the Best Container for Your Product
For the best results, make sure you are using quality containers with a consistent shape.
You may need to find a new container supplier. These are not always the suppliers with the lowest prices, but it is essential to find someone who specializes in what you need. Every company is unique, and it is important to find a supplier who has researched and understands those needs.
Problem #4 - Label Size & Material Issues
It’s not only the shape of a container that can be problematic. The material makes a difference too. If you notice label flagging or your labels are not fitting correctly, it may be a material issue.
Some questions to ask yourself are:
- Is your container glass or plastic?
- Are you using squeezable tubes or rigid plastic?
- Is your label too large to fit the container?
Choosing the Best Materials for Labeling Equipment
First, it is important to note that you should always communicate with your label converter and let them know what material you intend to use for your container. However, if you think the material may be where the issue is coming from, there is something else you can do.
To determine whether your label application issues are due to your labeling equipment or are a material issue, there are some tests you can try that can help you avoid ending up with thousands of unusable labels. This will allow you to evaluate which label face stock is compatible with your container.
Problem #5 - Wrong Adhesive
One of the most common issues experienced when labels aren’t sticking to their containers is the use of the wrong adhesive. Not all products are designed alike. If you notice uneven coverage on a pressure-sensitive label reel, such as missing pockets or too little adhesive present, this may be an adhesive problem.
Solving Labeling Equipment Adhesive Issues
Once again, it is important to make sure you are dealing with a supplier you trust and are keeping them updated with the materials you are using. Make sure they have detailed information about your current labeling process. This includes temperature and moisture conditions, as well as your container specifications. They should be able to help you make adjustments and prevent future issues from occurring.
Problem #6 - Labeling by Hand
Labeling by hand may work for many small businesses with limited products and customer bases, but as the business grows, you may want to try a new plan for labeling equipment. When demand grows, doing all labeling by hand can become overwhelming. It is more time-consuming and the application is less likely to be uniform. There is also more room for human error. If this sounds like your experience, it may be time to make a switch.
Updating Old Labeling Application Techniques
Instead of trying to label products all by hand, you can try automated label applicator machines. There are different options available. You may want to start with a tabletop label applicator which can be used in semi-automated mode. As sales continue to grow, you can easily switch to full automation labeling equipment.
Solving Label Applications Problems Before they Start
If you are just about to begin your labeling journey, it is best to avoid these issues altogether. Starting the process of choosing a labeling machine doesn’t have to be difficult. Pack Leader USA carries a wide variety of labeling machines for every need. There are also trained professionals who can assist you every step of the way. They also offer a free guide to help you along the way.
Explore your labeling equipment options today to find the right labeling equipment for you.
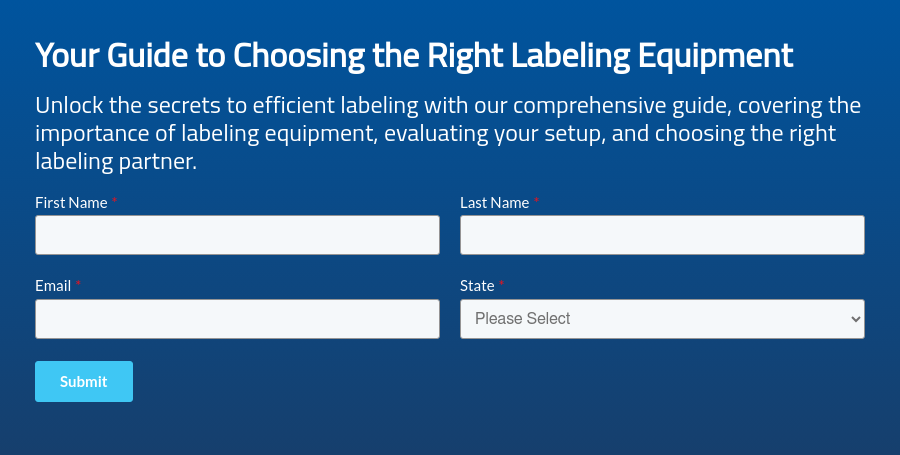
Resources:
- How To Fix Common Label Application Problems
- Top 4 Ways To Know You Have Quality Packaging When Labeling
- Where Things Can Go Wrong On The Application Line
- 3 Common Beer Bottle Labeling Mistakes
- Common Issues With Labels In High-temperature Environments
- 7 Common Problems When Using A Label Printer/Applicator
- Table Top Label Applicator Problems? It Might Be Static Electricity
- Hot And Humid: Label Problems And Solutions
- A Brief Guide To Label Converting Machinery
- Top 7 Triggers For Testing Your Label Material