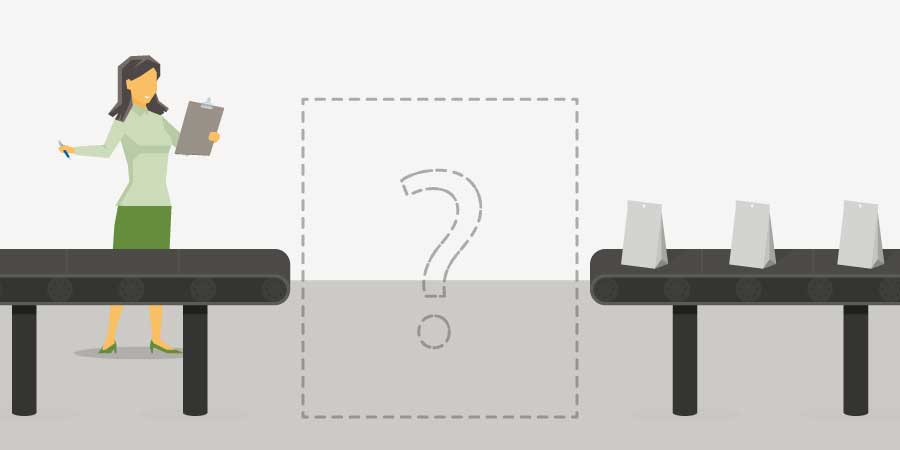
What are CBD facilities doing to get their products to market faster than others?
No CBD packaging line is perfect, but some are closer than others. Some facilities turn out high-quality products at seemingly breakneck speed, while others seem to be staffed by error-prone sloths. And on top of it all, no matter how legitimate production hurdles may be, the market isn’t going to sit around and let a company catch up to make everything fair.
So how can YOUR CBD packing line achieve that magical goal of increasing speed while increasing quality? Let’s go over four ways you can shape up, speed up, and get the results you desire, making your CBD facility the envy of the industry.
1. Evaluate Your Line
Before you can start improving your CBD packaging line, you have to identify efficiency benchmarks. It takes several steps to do this. To begin, measure the pace of each individual job to calculate the average time each should take. Then check that against the actual time each employee takes to perform those jobs. Measure the time the product takes to travel from one station to the other, too. Then add up your peak efficiency time, that is, the time it would take if every part of the production ran as smoothly as possible. Finally, add up the actual time for a product to move through the line and divide this by your peak time. You will now have a percentage representing your efficiency, which should be at least 80% of your goal.
Your raw materials need a closer look, as well. Look into whether you're paying too much for your CBD product ingredients and packaging, if they're incompatible with your equipment, and even if they take too long to get shipped to your facility. Quality should not be sacrificed, of course. Accusations of inferior products that have eschewed, reduced, or less effective ingredients hurt customer trust, destroy brand loyalty, and are a nightmare for a PR team. But if you can get lighter yet stronger packaging, for example, to save on shipping costs, then that's a victory for everyone involved.
Knowing efficiency benchmarks is a great place to start and even a trusted method for identifying big problems. Another way to determine issues, and ideally, root causes, is by asking “The 5 Whys.” Here’s an example of how this works.
Problem: My company’s CBD hand lotion isn’t selling well.
- Why? Consumers say it’s hard to find in stores.
- Why? Stores complained that our shipments had too many broken containers and stopped selling the product.
- Why? The containers were damaged in shipping.
- Why? The containers weren’t properly packed into the shipping boxes.
- Why? The employees weren’t trained in how to pack the containers to keep them from breaking during shipment.
By the fifth “why,” we’ve gotten to a root cause and can now address the underlying issue of employee training.
2. Track Everything
Once you collect your data on what needs to be fixed, it's time to start tracking everything you do. But tracking takes on several meanings:
- Tracking Your Materials and Shipments: You should know every detail about the items that come into and out of your facility. Haphazard storage leads to shipments getting lost, raw materials expiring, labels with old logos and incorrect information sitting around, and wasted time dealing with those things. Using a Warehouse Monitoring System will help keep your facility organized and in control of supply chain management.
- Tracking Employees: Track employee improvements as changes are implemented. If they were working at a subpar rate before, have they sped up without sacrificing quality? Are the right people in the right part of the line? Every worker has variability in their output, but studies have shown that merely placing employees at the right place for their skill level and work rate can dramatically transform a production facility's efficiency and effectiveness.
- Tracking Market Performance: As improvements are made, you should start seeing fewer returned products, fewer negative reviews from customers, and increased sales.
- Tracking First Through Tests (FTT's): Your production line should be more efficient, but that doesn't just mean faster. You should also see products of constantly high-quality coming off your line and with far less damage and problems along the way. No matter what your industry, tests are imperative to ensure you've done things right.
3. Optimize & Streamline
Streamlining your operation doesn't necessarily mean eliminating personnel; it could be optimizing processes and workflows to alleviate backups and wasted time. However, if a job requires two employees, don't force-fit one into the position. Doing this may save money in the short term, but it will overstress your employee and likely lead to costly mistakes in the long run. The better choice would be to either keep two employees on the job or consider automating a portion of that role.
You also want to be sure that machines performing consecutive functions are set up in the most practical way. If the equipment that cleans containers in preparation for the CBD oil is at the end of the line, but the filling and capping machine is in the middle, a simple order change could immediately speed things up.
Not only does every part of your process need to be in the right order, but you need to be aware of bottlenecks occurring. Bottlenecks show that one or more parts of your production line need extra assistance. Perhaps everything is going swimmingly right up until the labeling station. At that point, containers start piling up. This could be because they're waiting for an employee to hand label them, or your labeler can't keep pace with the rest of the line.
4. Automate
A human just can’t do things as fast or as accurately as a machine — this is where automation can make a big difference. While many companies make do with hand labeling initially, it’s wise to switch to automated labeling when packaging line pain points start to emerge.
Your label is the first impression most customers will have with your brand, and if they see crooked, torn, or bubbled labels that won’t stay on the container, they may assume the product is low quality, too. With a labeling machine, you can boost productivity by up to 500% while at the same time increasing label application quality. Some employees may fear that automation means they’ll be replaced. However, the truth is automation not only creates more jobs than it takes, but it also helps existing employees do their jobs better.
With automation comes maintenance, of course, but as long as you’re improving your processes, you can work in a preventive maintenance schedule, order kits of commonly needed parts, and train your employees on caring for and properly using the machines. Any manufacturer that supplies your equipment should offer training for your personnel as well as 24/7 service and repair. Any downtime is a hit to your profits, and if you can’t get your equipment repaired or serviced, then it may be time to get new equipment from a manufacturer you can trust to be there when you need them the most.
If you’re looking to make your CBD packaging line work better, consider the four ways mentioned in this post. And if you want to see dramatic increases in label application quality and line pace, it may be time to invest in an automatic labeling machine. To see how a label machine can transform your production line, read the article linked below, How to Label Products Faster Without Hiring More Employees. If you think that adding an automatic labeler or updating the one you have will help you work better and meet your output goals, check out our line of CBD labeling equipment.