There are many labeling equipment options available, but it’s up to you to choose the one that works best for your meal kit packaging line, food containers, shipment timeline, and budget.
Common Costly Packaging Line Problems
According to a Decision Analyst Survey in 2019, 76% of the manufacturers surveyed prioritized improving floor productivity as their most valuable growth strategy.
If you're experiencing any of the following problems, it might be time to upgrade your meal kit packaging line with better labeling.
Packaging line inefficiency
Inefficient packaging lines can delay distribution, affecting profitability and resulting in spoiled food and unhappy customers. Efficiencies can stem from many factors, but the most common is a machine's inability to accomplish a goal while minimizing time and effort.
Packaging line downtime
It's estimated that almost every factory loses between 5-20% of productivity due to downtime. Therefore, minimizing downtime in manufacturing is just as pivotal as maximizing quality and output to maintain contribution margins.
Packaging line bottlenecks
A bottleneck is a point of congestion that occurs when items move too quickly for the production process to handle. Sometimes companies are forced to slow packaging speed due to old or outdated equipment or methods, causing painful and costly delays.
Packaging line errors and waste
One of the most common ways businesses lose profits is through wasted products and avoidable errors. Waste is particularly problematic with older equipment and processes, which is why it's necessary to use consistently reliable machinery and methods to avoid waste and lost money.
According to a Decision Analyst Survey in 2019, 76% of the manufacturers surveyed prioritized improving floor productivity as their most valuable growth strategy.
If you're experiencing any of the following problems, it might be time to upgrade your meal kit packaging line with better labeling.
Packaging line inefficiency
Inefficient packaging lines can delay distribution, affecting profitability and resulting in spoiled food and unhappy customers. Efficiencies can stem from many factors, but the most common is a machine's inability to accomplish a goal while minimizing time and effort.
Packaging line downtime
It's estimated that almost every factory loses between 5-20% of productivity due to downtime. Therefore, minimizing downtime in manufacturing is just as pivotal as maximizing quality and output to maintain contribution margins.
Packaging line bottlenecks
A bottleneck is a point of congestion that occurs when items move too quickly for the production process to handle. Sometimes companies are forced to slow packaging speed due to old or outdated equipment or methods, causing painful and costly delays.
Packaging line errors and waste
One of the most common ways businesses lose profits is through wasted products and avoidable errors. Waste is particularly problematic with older equipment and processes, which is why it's necessary to use consistently reliable machinery and methods to avoid waste and lost money.
Solve Packaging Line Output & Profit Problems
The right labeling equipment can solve your meal kit packaging line problems by improving efficiency, eliminating downtime, keeping pace to avoid bottlenecks, and eliminating errors and waste.
Our guide will help you understand labeling equipment options and how to choose the right one for your line, meal kit packaging, label type, and budget.
The right labeling equipment can help you:
- Reach up to 85% efficiency with the right equipment
- Increase output by as much as 300% with an automatic labeler
- Keep pace by labeling up to 600 containers per hour with automation
- Save up to 20% annually in lost productivity with efficient line setup
Reach Up To 85% Efficiency
With the right equipment
Overall equipment effectiveness (OEE) measures how well a manufacturing operation is utilized compared to its full potential during the periods when it is scheduled to run. It identifies the percentage of manufacturing time that is truly productive.
An OEE score of 85% is considered world-class for manufacturers. While this is a reasonable long-term goal, an OEE score of 60% is more common. Anything less than 85% should serve as an indication that there’s room for improvement.

Increase Output By As Much As 300%
With an automatic labeler
Utilizing commercial labeling equipment has many benefits for any manufacturer with a packaging line. With labeling being one of the final steps in the packaging process, having the wrong machine in place could slow down your whole operation. On the other hand, having the right machine in place will dramatically increase output. This is why it’s critical to invest in the right equipment, including a labeling machine for your packaged meal kit food, if you want to reach and maintain maximum output.
Label Up To 600 Containers Per Hour
With automation
A rule of thumb for the labeling containers with a semi-automatic label machine is 400-500 containers per hour, depending on the machine and label type. Most packaging lines with fully automatic labeling machines can label 600-700 containers per hour.
Finding a semi-automatic or automatic labeler that can label 10-12 containers per minute will position your line for the fastest and most accurate labeling possible.
Save Up To 20% Annually In Lost Productivity
With efficient line setup
Productivity is a measure of the efficiency of an employee in converting inputs into useful outputs. To calculate productivity, divide the average output per period by the costs incurred or the resources consumed in that period. In doing this, you’ll discover how much productivity is lost annually. For many manufacturers, it can be up to 20%.
Lost productivity is most often a result of employees not being on the floor doing work due to illness, injury, or vacation. It can also come from employees' lack of proper training. When workers aren't adequately trained, it will automatically hamper time management and productivity. All of these are contributing factors to slowed production and loss of money.
Automation can help fix this problem. Machines can work at a constant speed, unattended, 24/7. That means the potential to package more food and meal kits at a higher quality continuously.
- 24/7 production
- More uptime, less downtime
- Reduced changeovers
- Labor cost savings
How To Choose Labeling Equipment
There are many different semi-automatic and fully automatic labelers available for food labeling, but it is up to you to find the one that works best for your packaging line setup, meal kit packaging, labeling type, and budget. All these variables will impact your labeling equipment selection. As you look for a labeler to boost efficiency, increase output, keep pace, and save production loss, consider these four things.
- Consider your current line setup and space restrictions
- Consider your container dimensions
- Consider your label application
- Consider your output goals
Consider Your Current Line Setup And Space Restrictions
Before looking at labeling machine options, consider your line current setup and determine the right machine size for the space you have. The right automatic labeler will fit your space, blend seamlessly into your existing packaging line, and keep pace with your other machines, making your meal kit food packaging process even more efficient.
The labeler you choose should also be able to grow with you, scaling along with your packaging line as it expands and improves over time.
The right labeling equipment will:
- Fit your space
- Blend seamlessly into your existing line
- Keep pace with your other machines
- Grow with you
Consider Your Container Dimensions
Knowing the size and shape of your food containers (pouches, bags, boxes, bottles, trays, cartons, etc.) and how those containers will be shipped (frozen, alongside an ice pack, etc.) will impact your label size, type, placement choice, and how the labels are applied to the container.
Consider Your Label Application
You know you need a dependable, fast, consistent, and budget-friendly labeler that will meet your packaging and output goals and fit within your current operational setup. But which labeler is best for your label application?
The most popular label types for food are wrap-around labels, front & back labels, top labels, top & bottom labels, and shrink sleeve labels.
Keep in mind that labeling machines come in various sizes and styles but are not necessarily universal to all label applications.
Wrap-Around: These are pressure-sensitive labelers designed to wrap labels all the way around cylindrical containers.
Front & Back: These machines apply labels to both the front and back of containers and pouches simultaneously.
Top: These machines apply pressure-sensitive labels to the top of a container, box, carton, or tray.
Top & Bottom: These labelers can apply labels simultaneously to the top and bottom of containers.
Shrink Sleeve: Shrink sleeve labels react to heat, causing them to constrict, conforming to containers tightly.
Consider Your Output Goals
When you’re looking for a labeler, be sure to keep your output and operations goals front of mind. Your labeler should be able to keep pace with the other machines in your line, helping to meet your business objectives and KPIs.
As you strive for greater line efficiency and effectiveness, the right machines will improve production speed and consistency — and help you to increase your profit margin. It’s time to get more meal kits out the door — and faster.
Choose a labeler that will:
- Help you to meet your production and operational goals
- Keep your KPIs on track
- Improve production speed and consistency
- Set you up for growth
Good Vs. Better Labeling Equipment
There's more to know about labeling machines. Being fully knowledgeable about your options will help you make a good labeling machine investment.
What's the difference between a good machine and one that would be BETTER for your meal kit service and packaging line? In this section, we'll dive into some specifics that will help you feel good about picking the right labeler for your needs, goals, and budget.
- Semi-automatic vs. automatic
- Tabletop vs. inline
- Quality construction
- ROI expectations
- Cost
Semi-automatic Vs. Automatic
Both semi-automatic and fully automatic machines automate label application. The difference between them is in how they are loaded and activated.
Semi-automatic labeling machines need to be hand-loaded for small product batches or integrated into your existing production line for fast labeling. The label is applied when triggered by a switch operated by a worker or a connected machine.
Automatic applicators can position containers themselves and apply the label. Some automatic label applicators can also reposition the container multiple times to apply several labels. No human operation is needed.
Tabletop Vs. Inline
The smaller, portable, and compact nature of this labeling equipment makes it perfect for tabletop use. These machines are most often semi-automatic and can be used as a stand-alone module or be incorporated into a packaging line. Tabletop labelers are ideal for meal kit companies that are hand labeling but want to start automating processes.
Inline labeling equipment tends to be larger, fully automatic, and offer more robust functionalities. Its conveyor effortlessly collects containers from one machine, labels them, then passes the labeled products to the next in line. This is a better option for meal delivery services that have large qualities to package and ship.
Quality Construction
Choosing quality-built equipment is a significant factor in keeping your operation running smoothly. Not only does your labeling machine need to fit with your other packaging equipment, but it should also produce little waste, prevent contamination, and work well for years.
A reputable and trustworthy labeling equipment manufacturer will conduct a quality inspection test and provide you with a certificate of proof. They should also have replacement parts readily available so you can have your labeling machine repaired promptly if anything should ever need replacing due to expected wear and tear.
And often, with investments, you get what you pay for: if it’s cheap, the construction is likely to be poor. The labeling machine you choose can significantly impact your meal kit packaging operation. It’s essential to evaluate the quality of the labeling equipment before you purchase to make sure you get the highest possible return on your investment.
Keep these notes in mind:
- Buy from a reputable and trustworthy labeling equipment manufacturer
- Expect a quality inspection test and a certificate of proof
- Well-made labeling equipment should last for YEARS
Roi Expectations
Though it may sound counter-intuitive, a recent manufacturing industry outlook report suggests that many manufacturers are looking to save money by investing in technology. Large manufacturing companies have reported that instead of cutting costs, they’re focusing more on operational efficiency. With productivity, technology, and standardization named as keys to success, more companies are turning to automation for the best return on investment (ROI).
Factors to assess now:
- What is the actual cost of your current labeling system, including equipment, materials, labor, downtime, parts, service, and wasted materials?
- Is your present system merely meeting your immediate needs, or can it grow with you as production increases?
- How quickly are you able to turn your product around using your current label application method?
- On average, how many labels are you applying each day?
Cost
The right labeling machine will deliver a positive ROI, but keep in mind your companies' current abilities and avoid over-buying. There is no sense in purchasing the fastest, newest labeling machine on the market if the rest of your production process is not fast enough to keep up with it. Instead, focus on finding a labeling machine that will meet your current needs and leaves plenty of room for you to scale up progressively but won't put a strain on your operation financially.
Generally speaking, semi-automatic machines start at about $15,000 and automatic labelers at $20,000, but both go up from there based on options and requirements.
Shop around and compare prices before committing to a purchase, and avoid burdening yourself with a system that is too big or expensive for your needs.
Whether you’re a start-up meal kit delivery service or you’ve been around for a while and need to upgrade to faster machines, keep your budget in mind as you make your labeling equipment investment.
Which Labeling Machine Is Right For Your Needs
Finding the right labeling machine that fits your specific needs may feel overwhelming, but understanding the differences will help you make an informed decision. Take a look at the following comparison charts to better understand the differences between our labeling equipment.
Check out our comparison charts.
Choosing A Labeling Equipment Manufacturer
Choosing the right labeling equipment is only the first step in setting up your packaging line to be more efficient, productive, and profitable. The next step is building a positive life-long relationship with your labeling equipment manufacturer and service team. Here's what you need to know about a labeling equipment partner before making a purchase.
- Industry reputation and expertise
- Factory acceptance tests
- 24/7 service and repair
- Parts availability
- Preventive maintenance
- Continuing education and training
Industry Reputation And Expertise
The labeling equipment manufacturer that you choose should have a trustworthy reputation among their customers across industries. Look for case studies on their website, a list of satisfied customers on their website, and their BBB rating.
At Pack Leader USA, we partner with our customers, helping them achieve their packaging line goals with the best-quality labeling machines on the market, including those in the meal kit service industry. It’s our mission to help all manufacturing companies push through packaging line challenges and succeed.
And to prove our commitment to high quality, all of our labelers are manufactured in compliance with Good Manufacturing Practices (GMP) standards and meet the strict ISO 9001 quality control procedures. We pride ourselves on making quality equipment.
Factory Acceptance Tests
Factory Acceptance Tests (FAT) help verify that newly manufactured and packaged equipment meets its intended purpose. The FAT validates the operation of the equipment and makes sure the customers' purchase order specifications and all other requirements have been met.
When Pack Leader USA conducts FATs, we invite potential customers to our facility so they can explore the equipment they're interested in with a salesperson and equipment tech, see a product run in action, and how it applies quality control guidelines. If the customer has more than one product, we'll demonstrate how changeovers function.
24/7 Service And Repair
Having a labeling equipment partner who can keep you up and running 24/7 is critical to your success. As you shop around for a labeler, be sure to ask about their service and repair plans and processes.

We have certified technicians on hand 24/7 to service or repair Pack Leader USA equipment by phone, web conference, or email. Because we're committed to resolving any problems you have, we'll send a technician to your facility to fix your machine if it can't be resolved through other means.
We understand how important it is that your labeling equipment works at all times. Downtime and waste are not an option for manufacturers trying to keep pace and meet output goals. You can’t afford unhappy customers or meal kit subscription calculations due to avoidable issues. That's why we're available and ready to help whenever you need us.
We'll also offer preventative maintenance plans that keep everything humming and equipment training for new personnel.
Parts Availability
Let's face it, even the best-built machines in the world require maintenance if they are under constant use. And proper maintenance demands easy access to new parts. When parts eventually wear out, such as drive belts, bearings, and motors, can you count on your automatic labeling machine manufacturer to have them in stock near you for immediate shipment?
Pack Leader USA distributors all over North America carry spare parts kits, accessories, and components for all our machines — plus many are available through our secure online store. Genuine Pack Leader USA parts are built to work best in your machine and are backed by our industry-leading warranty.
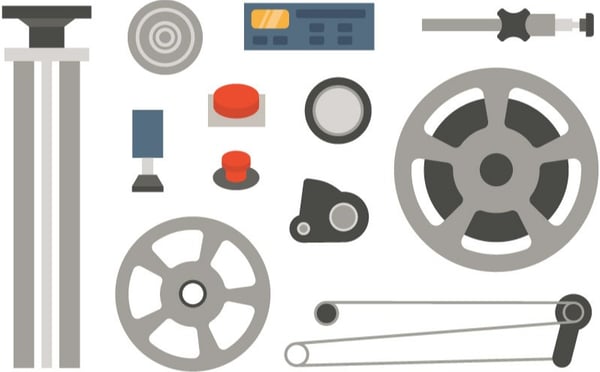
Preventive Maintenance
By detecting incipient flaws and repairing and replacing parts before they fail, preventive maintenance helps you avoid downtime, saving money in the long run.
Pack Leader USA and authorized distributors offer our Pack Plus Program to customers. This preventative maintenance program includes a 50-point machine inspection to ensure your machine is running at optimal efficiency. With this plan, you should feel confident that your labeler will be running in ten years as well as it did when it was first delivered.
We stand by our equipment, and we strive to keep it in great shape so you can be empowered to stay focused on your business — getting fresh and tasty food into the hands of your meal kit customers fast.
Continuing Education And Training
Employees come and go, and products may change over time, so finding a labeling manufacturer that offers continuing education and training is crucial to a great partnership.
We offer continuing education and training for new employees to ensure they are fully educated on Pack Leader USA equipment. In addition, if your company has a new labeling project that has not been set up on the existing equipment, we can analyze that it is compatible with your machine. Our technicians can also train employees on any new equipment set-up. We can do this through a web conference or in-person training by one of our certified technicians.
Why Pack Leader USA Labeling Equipment
As our name suggests, Pack Leader USA is a leader of the pack in the labeling industry. Built on the research and development of Pack Leader Machinery, Inc., we entered the North American market with high-quality products, modernized labeling technologies, and an excellent customer service reputation. We have taken the labeling industry to the next level by designing easy-to-use and cost-effective labeling machines that serve the growing meal kit delivery industry.
We are committed to providing our customers with reliable machinery, quick service, and readily available parts to ensure uptime and eliminate costly downtime. Before you purchase, we are happy to offer a free consultation. If you’re ready to buy, we’ll walk you through the purchasing process step by step from price quote and delivery to ongoing customer support and training.
We promise to provide more than just a piece of equipment for your production line — we’ll come alongside you as your partner.
Our Process
- Quote
- Order
- Production & Customization
- Delivery
- Setup & Training
- Ongoing Support
Our Labeling Equipment
Get Your Free Labeling Consultation
Set up a free labeling equipment consultation with our team today to learn which of our labelers can help your meal kit delivery operation improve productivity and efficiency and fit your budget.
Or call 1.816.256.5647